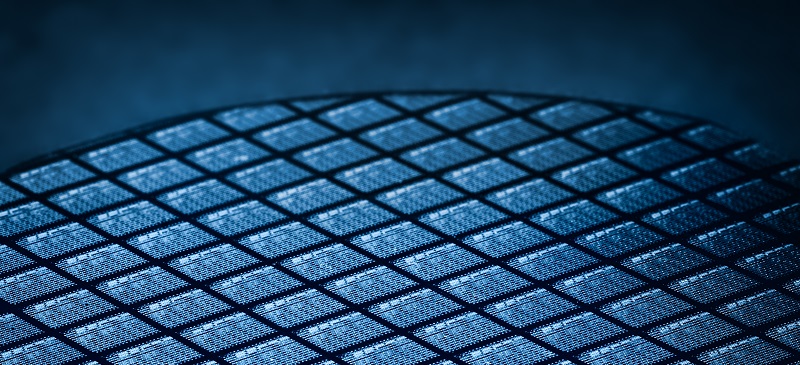
Semiconductor Trends to Watch in 2018 (and Why They Emphasize a Need For Premium Equipment)
In 2017—a year that was characterized by the adoption of the Industrial Internet of Things and Industry 4.0 technologies—semiconductor revenues reached record highs, largely due to such technological innovation. While these mega trends will no doubt continue to shape the semiconductor industry for years to come, if we look toward the next 12 months we can glean specific insights – those that fabs can start to capitalize on today to achieve higher levels of operational efficiency and quality, quickly.
Let’s take a look at the trends that could dominate the semiconductor market in 2018.
Trend 1: Optimizing Semiconductor Processes Through Analytics
A report by McKinsey reveals that approximately 80% of semiconductor development projects are unable to meet their initial production schedules, often due to the fab’s overestimation of their ability to handle complex tasks or an underestimation of the time required to complete work. Often they are understaffed in the early and late stages of the project, and end up overstaffing the middle phase to compensate. Applying advanced analytics is a way to take the guesswork out of predicting productivity to ensure the right resources are deployed at the right time throughout the development lifecycle.
Similarly, when it comes to semiconductor manufacturing, the use of analytics can yield accurate insight into equipment health and ensure the right systems are running at peak performance when they are required. By collecting data on certain indicators of a gas delivery system’s operating condition, for example, fabs can predict when maintenance will be needed and reduce unplanned downtime.
Beyond preventative maintenance, fabs can also use analytics to hone equipment performance in ways that optimize their output. The McKinsey report above references a company that linked its equipment and inspection data to predict process failure in a production step that involved depositing material on a wafer with 70% accuracy, helping to prevent significant yield loss early in the production process.
For semiconductor fabs to capitalize on the analytics trend, they will need premium equipment solutions with built-in sensing capabilities and that are equipped with advanced control technology. This way, operators can quickly act on collected sensor data and fine-tune system performance in real-time.
Trend 2: Acquiring Exactly the Right System for Semiconductor Fabs
In 2017, the semiconductor industry is expected to close with an all-time spending high of $55 billion in fab equipment spending – a 37% increase from 2016. This spending trend is predicted to continue through 2018, leading to an estimated year-end total of $58 billion.
This trend indicates that many fabs are expanding, but smart fabs will still focus investment in equipment that sets their processes apart. That means choosing systems that not only uphold necessary SEMI S2 compliance, but also work to improve overall process performance. When it comes to gas delivery, fabs will be seeking systems that can deliver the exact specialty gases and mixtures they require, in the exact pressure, temperatures, and flow rates their application demands, so that they can ensure the best output possible and ultimately strengthen their competitive edge in a growing market.
Trend 3: Evolving Semiconductor Innovation
Since the early days of semiconductors, Moore’s Law—the prediction that the number of transistors in a dense integrated circuit doubles every 18-24 months—has held true. However, in recent years, scientists have increasingly come to believe that fundamental physical limits may soon make it difficult to place additional transistors on the same small area in an economical way, which could ultimately prove Moore’s Law faulty.
With transistor density possibly soon reaching its physical limit, fabs must find other methods for adding additional storage, processing, and transmission capabilities into semiconductor technology. As processes evolve, equipment that can be customized to flexibly respond to various semiconductor manufacturing innovations will become increasingly important. Fabs will need to find equipment partners that are able to adapt their standard systems through custom engineering processes, to ensure their equipment can rise to the challenge of supporting new, innovative manufacturing approaches.
AES: A Provider Prepared for the Future
As the semiconductor industry continues to evolve, gas delivery systems must advance to handle ever more complex applications. That’s why AES is focused on supporting Tier 1 leaders with dynamic, flexible, secure systems that leverage tomorrow’s advancements, today. Want to learn more about how we are engineering our gas delivery solutions to address the trends above? Talk to our team today.
Share this Post: