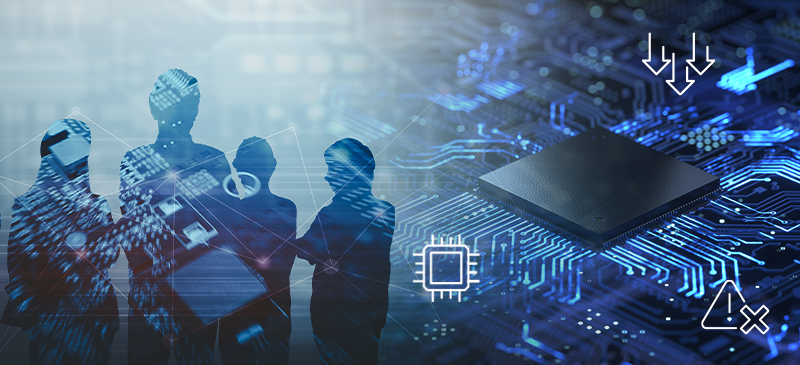
The Semiconductor Skills Crisis Continues: Latest Developments and Strategies Update
Even after several years, the semiconductor skills shortage continues to evolve, introducing new considerations for the industry at large. In our previous blog post, we discussed the top three takeaways from the ongoing skills shortage and its implications for the industry. Since then, the challenge of filling semiconductor roles has only become more urgent.
New reports reveal that by 2030, more than 1 million additional skilled workers will be required to meet the ever-growing demand in the industry. As we dive into the current state of the talent shortage, we discover that the need for talent extends beyond the United States affecting semiconductor manufacturing, innovation, and supply chain stability across the globe. In this blog post, we will delve into the latest updates regarding the skills shortage and review some strategies your fab can take to overcome short-term hurdles.
Tracing the Roots of the Semiconductor Skills Shortage
The semiconductor skills shortage has become more pronounced in recent years, affecting not just the U.S., but Europe and Asia as well. Over the years, semiconductor manufacturing reduced its investments in technician training, and instead focused on STEM education and research funding, reducing training opportunities for technical semiconductor roles.
Between 2018 and 2022, job postings for semiconductor technical roles in the European Union and U.S. rose at a significant CAGR of over 75%. Unfortunately, this surge in demand is not met with an equal amount of supply. Fewer than 100,000 students enroll annually in programs for electrical engineering and computer science—fields that are essential to the semiconductor industry. In addition, roughly one-third of the U.S. semiconductor workforce is nearing retirement. With the aging workforce and so few graduating with the required skills, there is not enough talent to fill these gaps.
Looking Ahead at the Numbers: The Increasing Demand for Engineers and Technicians
The U.S. domestic semiconductor manufacturing workforce has seen a steep decline, dropping 43% from its peak employment levels in 2000. Currently, the semiconductor industry gains about 1,500 engineers each year, which is only 3% of engineering graduates. With projected engineer demand up to 88,000 by 2029, these small numbers present a huge potential problem for semiconductor organizations.
The outlook is equally concerning regarding technicians. Only about 1,000 new technicians enter the semiconductor field annually, with the demand expected to reach 75,000 by 2029. The combined shortage of both engineers and technicians could total anywhere from 59,000 to 146,000 workers by the end of the decade.
As early as 2025, the demand for semiconductor talent is expected to rise drastically. The annual demand for engineers is expected to increase from 9,000 to 17,000, and the demand for technicians will rise from 7,000 to 14,000. By 2027, demand will peak at 20,000 engineers and 17,000 technicians needed, highlighting it as one of the most pressing challenges for the semiconductor industry.
Three Critical Investments to Help Bridge the Gap
To combat the growing talent shortage, organizations must adopt strategies to attract, develop, and retain talent. Below are three investment areas that could change the game for your fab in the short term.
- Invest in Emerging Talent Development Programs
Companies can partner with educational institutions to create specialized training programs and fast-track certifications in semiconductor technology. Apprenticeships and internships can also be expanded to give students hands-on experience, while upskilling initiatives for current employees can help close the skills gap from within. - Invest in Automated Technology
Organizations can improve efficiency within their fabs by optimizing automation, deploying AI-driven solutions, and cross-training existing workers to handle multiple roles while minimizing tedious tasks. By maximizing the productivity of the current workforce, businesses can mitigate the impact of the shortage while they build up their talent pipeline. - Invest in the Right Partner
Navigating the skills shortage requires more than just internal efforts. Having the right partner can make all the difference. These knowledgeable partners have a unique skill set and experience that can help companies remain competitive and compliant, while maintaining the standard of excellence your fab requires.
Bridge the Gap with AES
In a fast-paced, ever-changing industry, it is paramount to stay ahead of the curve and ensure your equipment can handle evolving industry needs in the long run. As we have noted, with the right partner, you can do this and more. AES helps your organization improve its semiconductor fabrication process by providing tailored solutions specific to your application’s needs. With an experienced team of industry experts, we are there to support you every step of the way, ensuring your business has the tools you need to meet the industry standards of today and tomorrow.
Contact us to learn more about how you can future-proof your fab and position yourself to thrive in an increasingly competitive semiconductor landscape.
Share this Post: