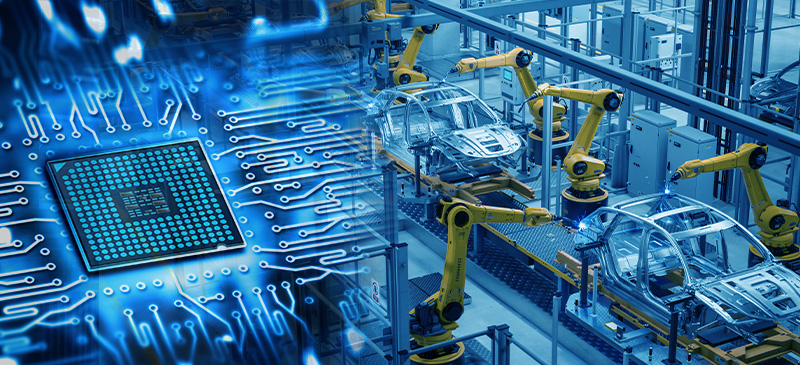
Navigating Complexities: The Semiconductor Shortage’s Effect on the Auto Industry
There has been seemingly no limit to the number of industries affected by the persistent semiconductor shortage. The automotive industry has been one of the hardest hit, as semiconductor chips are crucial for today’s car manufacturing process. As a result, more than 11 million vehicles had to be removed from production in 2021 due to the shortage. Consequently, global car sales in 2021 were down by more than 12 percent compared to 2019, resulting in a loss of ~$210 million USD in revenue for the global automotive industry.
The chip shortage has obviously had a tremendous impact across many industries, with the ever increasing reliance on these chips introducing many problems related to supply and demand. In previous blog posts, we looked at the CHIPs Act, the problems the shortage had caused, and the outlook of the chip shortage in 2024. In this blog post, we will focus specifically on the auto industry, the effect the shortage has had on it, where the industry stands today, and what actions are being taken to balance supply and demand.
The Shortage’s Origin
The microchip supply issue has been ongoing since the COVID-19 pandemic due to a series of contributing factors, including the long wait on the crystals for silicon wafers to grow. These crystals are a part of a 700-step process to assemble microchips, which takes about 14 weeks to complete. A majority of those weeks are spent growing the crystals, and their growth cannot be accelerated.
Because products that require chips are somewhat time-sensitive, as they include features that are only considered “new” and “exciting” for a certain period of time, their demand continues to fluctuate. The ever-evolving product innovations motivates OEMs and Tier 1 suppliers to utilize a “just in time” methodology for manufacturing to produce just enough to optimize costs and meet demand.
With the electronics industry making up the largest market share of chips, the auto industry ranks the second largest, at 15%. This means the majority of chips are being used for 5G and other electronic product development, while the auto industry is creating architectural changes, necessitating a higher quantity of chips that are more advanced.
The Shortage’s Effect on the Auto Industry
In 2021, the shortage lost automakers billions of dollars, as they were forced to reduce production volume and cut popular features from their vehicles. There were additional production cuts due to other factors, such as a personnel shortage coupled with America’s reliance on suppliers in Asian countries. Carmakers cut 19.6 million vehicles from production between 2021 and 2023, with manufacturing leads times skyrocketing to 10-12 months from their normal 3-4. Recent improvements in production capacity are not enough to improve supply to meet high demands. Time-consuming hurdles such as manufacturing slowdowns, shipping delays, and lack of material all contribute to the supply chain issues surrounding the shortage.
The automotive industry is also experiencing issues from the demand perspective. Shipments of semiconductor units for automobiles increased between 2020 and 2021 and will only continue to increase with the growing prevalence of electric cars, which utilize more semiconductors than other vehicles. Additionally, East Asian countries currently make up 88% of the semiconductor market, holding a surplus of all supply. As facilities are built and expanded in the U.S., American companies will still be reliant on manufacturers in Asia in the near future. Prices are climbing as well: the average modern car requires 1,400-1,500 chips to function, and some cars require up to 3,000. In 2020, this cost was around $500 per car, and is projected to increase to $1,400 per car by 2028, as they will require more chips.
Though the chip supply is finally improving, the long shortage period has caused a new issue. Not only has the production of vehicles drastically decreased from the year’s original forecast, but the cars that have been manufactured can’t be transported due to a rail car shortage. With an increase in automotive sales, the U.S. wasn’t prepared to handle the increase in production that came with it.
The Current Status of the Auto Industry
Before the pandemic, the trajectory for global vehicle production to reach 100 million units annually was slated for 2022, but is now expected after 2030. Therefore, the auto industry has to adapt to the new supply level and manipulate how they use their supply to achieve higher sales.
By mid-2023, however, we saw significant progress. Current supply levels allow production of 22 million units of light-vehicle production every quarter and the number of units lost in 2023 mid-year are significantly lower than in 2021.
Semiconductor supply is on the up and up, no longer a major obstacle for vehicle production. Regardless, experts predict that the shortage itself may still persist for the next 3-5 years.
Decision-Making for the Future of Auto
The chip shortage led companies to find workarounds for their manufacturing plans, as it became more difficult to obtain enough chips to meet demands and production needs. These adaptations came in many forms, from rewriting software to adjusting shipping processes. But the inability to obtain enough chips for their products forced companies to manipulate their machines to deliver the best possible product without including many features.
This comes with a number of sacrifices and lingering questions: Is it worth creating similar products that lack certain features that require more advanced chips? Will consumers buy the product without all of the potential features, and be willing to add them later? Is it worth the additional cost?
In an effort to meet demand and make adaptations to the manufacturing process, the auto industry is making a habit of ordering chips in a surplus. With this effort, the additional 10-20% of chips will act as backup inventory for demand relief—but fulfilling these orders will take time. Additionally, the U.S. is taking the initiative to develop its own plant in order to rely less on Taiwan.
A Strong Partnership to Nagivate through Challenges, Together
As the industry continues to address the chip shortage, the growing number of adjustments to processing and manufacturing can be overwhelming. It’s crucial to secure a partnership with an industry expert who can meet you where you are and provide you with a unique set of tools to thrive in an ever-changing world.
AES can serve as that partner. Reach out to us to speak to one of our UHP gas delivery experts today.
Share this Post: