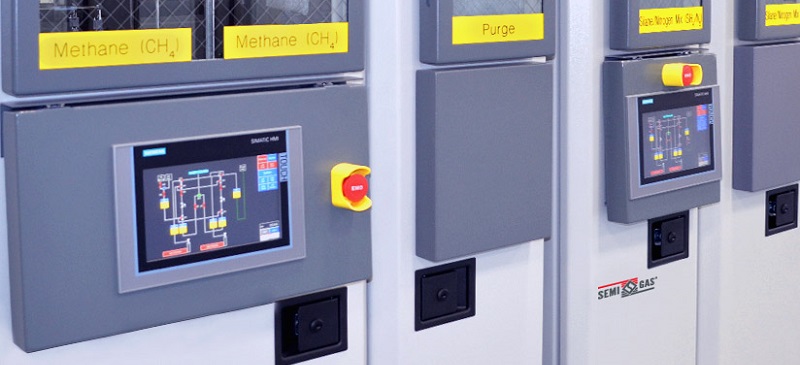
Human Machine Interfaces: Designed with People in Mind
In today’s increasingly automated world, those working in industrial, manufacturing, and research environments interact with machines constantly. Human Machine Interfaces (HMI) refer to all of the touchpoints that occur between a person and a machine, and proper HMI design is critical to enabling safe, optimized operation and monitoring of systems that power advanced processes.
Effective HMI design for gas delivery systems must address several key aspects related to the ergonomics, user interface (UI), durability, precision, and most of all, safety of the controller being developed. Recent advancements in component technology now offer controls engineers a plethora of design options, not only for the electromechanical and tactile elements of the interface, but also for environmental sealing, mounting style, size, illumination, and overall appearance. Below we take a closer look at several key considerations driving HMI design today.
Safety: Priority #1, 2, and 3
Automated machinery is helping users across industries significantly improve efficiency, but is also creating more system complexity which in turn creates greater safety risk. For that reason, HMI systems must be able to ensure safe, error-free operation, even under the most adverse conditions. It is important to design controllers to industry standards that are specific for the environment in which they will operate, as these standards often drive the safety features, functionality, and design attributes that will need to be incorporated.
Ergonomics: Ensuring Easy, Intuitive Operation
Poorly designed interfaces not only adversely impact productivity, but can lead to occupational diseases and safety accidents. HMI design, backed by a full understanding of how users are intuitively driven to interact with the systems they operate, is of the utmost importance to developing an ergonomically optimized controller. For example, mushroom-head pushbuttons make for intuitive on/off switches because of their large, distinctive shape and ability to be quickly activated with a palm slap, even wearing gloves. Additionally, grouping indicators or switches by their operation on the controller face helps users quickly identify and interact with the right components for the task at hand. With the proper ergonomics, you can help ensure the controller is operated in a consistent, predictable manner.
Intended Use: Understanding Its Application
The manufacturing environment and application of the system that the HMI controls should also shape component selection. When designing for semiconductor and electronics production, for example, interactivity and full functionality like color touchscreens are vital factors, as control terminals perform discrete functions and require very precise and flexible operator oversight to ensure continual system optimization. In research environments, users may be less familiar with the ins and outs of system operation, and therefore a simple, user-friendly interface will be most valuable. Equipment operating in a clean production environment needs an HMI system that is sealed against the ingress of fluids and particles, while still making user access and operation easy. As you can see, operating realities are a driving force in optimal HMI design.
Form Factor: It Can Work Well, and Look Good Too
New HMI technologies are allowing controls designers to evolve the quality of their interfaces, reflecting more of the modern styles that users see in the other devices they interact with each day, from their smartphones to remotes. While elements like illuminated pushbuttons, toggle switches, indicators, and selectors will remain essential components for a controller’s primary functions, more and more systems are now able to integrate capabilities to visualize production processes and status, leverage touchscreen controls, and more. The use of high-grade plastics and metals not only improves the look and feel of the controller, but enables designers to achieve very close tolerances and exacting calibration – ensuring the interface’s performance is as advanced as its design.
At AES, we understand the impact that effective HMI design can have on the overall operation of, and operator satisfaction with, our gas delivery systems. We never let control technology be an afterthought in our equipment engineering, and undertake a comprehensive review of your application, functional requirements, and needs of your users to choose and tailor the right HMI system from our line of SEMI-GAS® GigaGuard™ and VERSA-GAS™ vRun™ controllers.
Share this Post: