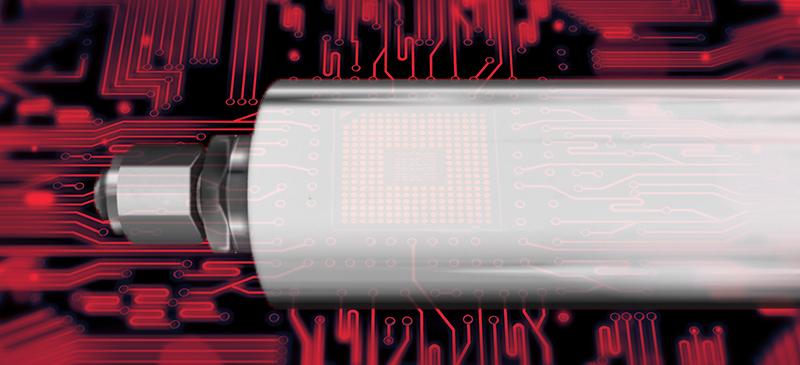
How to Properly Purify the Gases that Power Today’s Technologies
Precise and reliable gas delivery is a crucial part of semiconductor manufacturing. And with today’s increased costs of manufacturing semiconductors and the recent semiconductor shortage, time can simply not be wasted on compromised gas purity.
Semiconductor manufacturing is a complex process where multiple gases in varying flow rates are carefully delivered to process chambers in order to produce critical features on silicon wafers. To support today’s vast and varied applications, these gases must not only be delivered in precise quantities, but they must also maintain strict purity levels.
As semiconductor technology continues to evolve, adhering to stringent requirements for precise and pure gas delivery has never been more important. Even a trace level of contamination can render a chip useless, which can lead to a multitude of unwanted costs. And those costs are getting greater and greater. In the past few years, research and design costs for the development of a chip have increased from about $28 million at the 65 nanometer (nm) node to about $540 million at the leading-edge 5 nm node. Fab construction costs for the same nodes have also increased from $400 million to $5.4 billion, according to McKinsey.
Why Gas Purity is So Important
For fabs, where the quality of gas used in a process is intrinsically tied to yield, the gas purifier is an integral part of the equipment landscape. If gases introduce contaminates during production, there can be severe ramifications for process quality and system integrity.
Selecting the right purifier for high and ultra high purity applications is shaped by various specifications, like gas type, impurity, pressure, and flow rate. There are four key areas to look at to ensure your gas is pure and that the right kind of purifier is being utilized for your specific applications.
- Determine the properties of each specific process gas involved. A gas purifier’s role is to remove trace impurities from process gases to ensure contaminates do not impact production. Doing so requires gas purification technology that can remove impurities down to the parts per billion (PPB), or parts per trillion (PPT) level. Different gases have different properties—with some that are highly flammable, hazardous, or toxic. Common process gases include NH₃, CO₂, H₂, SiH4, HBr, Cl2, BCl3, DCS, and PH3, and there’s also a wide range of other gas types that can be used, like purge, passivation, and fluorinated gases. The ideal purifier solution is designed with the properties of each specific process gas in mind, accounting for factors that may impact their stability during production.
- Optimize the purifier for your unique flow requirements. Pairing a gas purifier that’s optimized for one flow rate with an application that demands another flow level can result in poor purification and compromised safety. The purifier solution should be tailored to your unique flow rate requirements in order to achieve the standards for purification and performance that your application demands. Once a fab has identified the volume of gas needed, the next step is to consider the type of purifier to use—point of-use, micro-bulk, or bulk. Each purifier can be used in isolation or in a series with others based on gas stream, level of impurity, and outlet purity required. For example, bulk purifiers operate at the ultra high purity level, making them ideal for UHP applications like semiconductor fabrication.
- Ensure the purifier meets pressure and temperature demands. You should know your application’s precise pressure and temperature demands, as both will impact your purifier selection. Pressure varies by gas type and process application, and there are additional requirements for use at elevated temperatures that vary based on gas type, targeted impurity, and function. The right purifier solution should be tailored to the specific pressure and temperature requirements dictated by your application.
- Perform preventative maintenance to keep purifiers working optimally. Gas purifiers don’t last forever, as they are designed for continuous operation and will eventually reach end-of-life. When installing a purifier, making a commitment to preventative maintenance is key to ensuring the purifier always operates at its optimal level. You should put your purifiers on a preventative maintenance schedule and then make decisions related to replacing or regenerating them prior to the lifetime of the unit expiring.
Positioning Fabs for Success
Today’s semiconductor fabs cannot afford for impure gases to disrupt their demanding manufacturing operations. Choosing the right purifier for your needs is absolutely critical in today’s demanding and complex tech climate. ARM Purification delivers a full range of point-of-use, micro-bulk, and bulk purifier solutions for high and ultra high purity applications that reliably uphold mission-critical gas delivery requirements across today’s newest technologies and applications.
Learn more about how the right gas purifier can enable your semiconductor fab to meet today’s rigorous industry demands.
Share this Post: