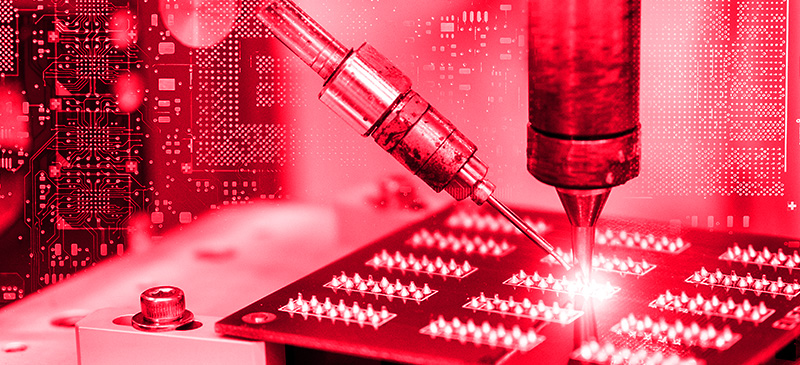
High Volume, Higher Standards: Key Areas to Consider when Choosing a High-Volume Bulk Gas Delivery Solution for Semiconductor Fabrication
Precision gas delivery is extremely important to semiconductor manufacturing. Various gases in varying flow rates are delivered to produce features on silicon wafers used in manufacturing chips. And with semiconductor manufacturing at critical supply chain and intricacy levels today, it’s crucial to deliver these gases in precise quantities with excellent repeatability and stringent purity levels.
Even with the current semiconductor shortage, the global semiconductor market is projected to keep growing—with growth skyrocketing to $803.15 billion in 2028 at a CAGR of 8.6% in the forecast period of 2021-2028. And as semiconductor technology gets more intricate, and transitions to advanced nodes below 5nm, the requirements for process gas accuracy, repeatability and contamination-free gas delivery have become paramount. The safe distribution and delivery of bulk hazardous process gases is critical today, and semiconductor manufacturers must choose an affordable and trusted solution for bulk delivery of specialty ultra high purity gases.
This blog post will explore some key areas to consider when choosing a bulk gas delivery solution.
Consideration 1: Compliance
Over 100 gases are used in semiconductor manufacturing today, and SEMI Standards—the basis for semiconductor equipment safety programs—maintains a comprehensive database of all gases used. It’s important for semiconductor equipment to remain in compliance with all industry standards, so make sure that your chosen bulk gas delivery system upholds rigorous standards for safety and design. For bulk gas delivery equipment, systems should comply with requirements for hazard alert labels, safety interlock systems, emergency shutdown, hazardous energy isolation, seismic protection, and more.
Consideration 2: Safety
Safety is paramount when dealing with the bulk delivery of specialty ultra high purity gases, especially as many hazardous chemicals and gases are used every day in the fab. Further, it can be difficult to ensure the health of workers due to widespread use of trade secret ingredients and a lack of hazard information, so the commitment to safety is critical. As bulk delivery systems support higher flow rates, they also come with engineering hurdles that must be overcome. There are unique thermodynamic challenges when handling larger flows, and as a result, safety and reliability can be compromised by under-equipped delivery solutions. You should ensure your ideal system supports safety initiatives and requirements.
Consideration 3: Quality
Ensuring quality when fabricating semiconductors is a must. Quality management is a key for increasing the competitiveness, productivity, profitability, and sustainability of the fab. Historically, the ceiling for test is 2% to 3% of the total chip budget—but budgets have been edging higher in recent years, so it’s important to maintain high quality is high to keep costs down. With an efficient and proven bulk gas system in place, quality can be ensured.
Consideration 4: Reliability & Redundancy
Uptime is a critical KPI for today’s fabs. Through complete redundancy, fabs can ensure that bulk gas delivery systems never go down unexpectedly. A winning solution will have multiple controllers on a cabinet, so the system is not reliant on a single control technology. In addition, these controllers will be able to both operate independently and interface together with controllers on other systems to orchestrate processes efficiently.
Consideration 5: Affordability
As supply chains slow and costs rise, it is important to focus on value when choosing a gas delivery partner. Semiconductor chips are complex to make, and not all chips from the same wafer may operate as desired. These defective chips are discarded, lowering semiconductor yield while increasing production cost. In fact, the semiconductor industry rejects around three million wafers every year, costing billions of dollars. A high-quality gas delivery system, however, can ensure precise outputs and reduce costly waste.
Ensuring Your System Meets these Key Requirements
You should make sure your system meets these necessary requirements. If not, look to a new solution. All of these essential considerations can be found in SEMI-GAS®, which serves industries with demanding ultra high purity requirements. SEMI-GAS works with those who are seeking premier, production-ready gas delivery and distribution solutions that are globally renowned for quality, and capable of meeting the most rigorous needs for precision and purity. Why you should choose SEMI-GAS:
- SEMI S2 Compliant. All SEMI-GAS® equipment upholds the requirements of this cornerstone safety guideline for semiconductor fabrication facilities, making them proven in practice to provide the highest levels of precision, purity, and operator control.
- State-of-Art Control Technology. SEMI-GAS® products are equipped with our premier line of UL-labeled GigaGuard™ controllers, which feature intuitive operation and the utmost control needed for advanced production environments like yours.
- Analytical Tested and Approved. SEMI-GAS® systems undergo sampling validation testing to ensure purity standards of less than 100 ppb for Moisture, Oxygen and Total Hydrocarbons, and less than 5 Particle counts per cubic foot at the 0.1-0.3 um range, so you can be sure our gas delivery systems are of the highest quality.
Click here to learn how SEMI-GAS® empowers semiconductor innovators to capitalize on opportunities for differentiation. Click here to read the ‘High Volume, Higher Standards’ infographic.
Share this Post: